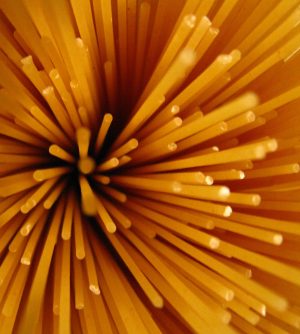
Reduction of product losses on pasta production lines
This practice descibes how simple measures can support reduce the material losses, and increase the productivity within a pasta handling and loading systems.
This section compiles a database of more than 200 resource efficiency measures that were identified using the TEST methodology and successfully implemented within several industries across many sectors. The measures are classified by sector and subsector, type (good housekeeping, process control/modification, technology change, etc.), category of resource savings (water, energy and/or materials), scope and applicability (process or utilities). The database enables the use of predefined filters including the possibility to use keywords for an advanced search.
Each measure in the database includes a description of the problem, a technical description of the solution, the economic and environmental benefits quantified for the specific company case, the costs and the expected return on investment, suppliers of equipment as well as other aspects related to safety, maintenance, productivity and technical implementation.
This practice descibes how simple measures can support reduce the material losses, and increase the productivity within a pasta handling and loading systems.
Material losses were eliminated within this couscous production line through good housekeeping measures.
Within feeding of the production lines from the silos, high amount of rejected material was quantified. As cause of this loss was identified lack of proper cleaning of silos including lack of maintenance / regular replacement of membrane at the bottom of silos.
Measurements of surface temperature within the steam network revealed lack of maintenance for the network, particularly in the pipes insulation. This resulted in overconsumption of fuel in the boiler. Fixing the insulation shall increase the boiler efficeincy, and reduce the energy consumption.
Gaseous effluents from a chemical company contain traces of sulphur dioxide, that result in the effluents exceeding the environmental limits. Directing the effluents to a catalytic conversion tower allow for oxidation of sulphur dioxide to SO3, which can be directed to the production. Nevertheless, the hot air from the effluents will be utilized for the reaction.
Production stops in a metal packaging manufacturing facility are due to interuptions in the supply of pallets from the store to the production site. Reviewing the procedures for transfer of material, having the raw material supply within the priority of forklift drivers, and assuring strategic stock of raw material within the production hall eliminates those interuptions, providing production gains.
Due to its obselete design, the boiler de-aerator of a beverage company was not functioning properly leading to over consumption of energy in the boiler, and increase corrosion within the steam network. Changing the de-aerator with an updated design shall allow complete removal of air and incondesible gases from the condensate, saving on energy consumption
Mapping the cause of high warranty claims in a battery manufacturing company revealed that major cause is loose welding of battery terminals. Setting a quality control procedure, training the staff, and maintaining the welding machines and tips reduces those claims, and consequent market returns.
Due to the frequent product change over in a dairy to meet the market demand, the company runs CIP to assure suitability of the production line. Reviewing the production plan to assure the suitability of at least one product change without the need of cleaning saves on raw material, water and energy, as well as increases the availability of the production line.
This practice represents the case where the boiler was of old low efficiency model, and sized to match the full load of the production line, which rarely occurs. Reviewing the load pattern of the production line, the boiler can be replaced with smaller models, increasing the load factor, and thus the boiler efficiecny. Having the new boilers connected in parallel also provides operational flexibility. another benefit from this upgrade is the fuel switching from the heavy fuel oil existing boiler to diesel fired boiler, which is more economic and have less environmental impact.